Reduce Value Chain Emissions From Industrial Facilities
Environmental Defense Fund
Emissions from industrial facilities in your value chain can represent a significant share of your company’s total footprint. Encouraging your suppliers to implement strategies to save energy and reduce gas leakages can lower their operating costs and help you realize your emissions targets.
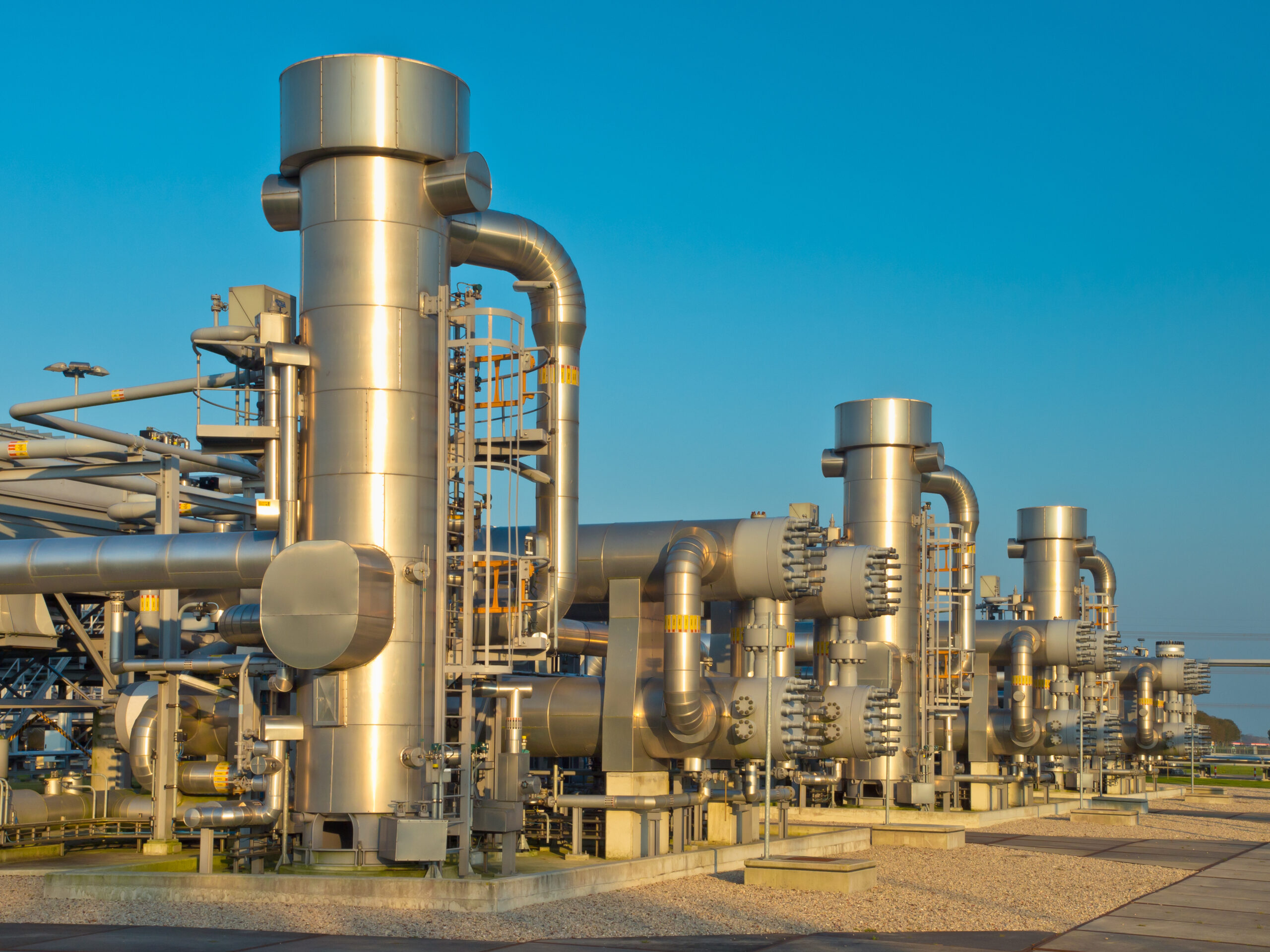
Industrial facilities are responsible for a significant share of global greenhouse gas emissions. Addressing industrial emissions has become a top priority as climate concerns grow. Industrial facilities can also contribute to air and water pollution, which can have negative health impacts on nearby residents, particularly low-income and marginalized communities. Supporting your suppliers in reducing their industrial emissions can have social, environmental and economic benefits.
Energy use and refrigerant and gas use is essential to the operation of many industrial facilities. However, some basic and cost-effective strategies can be deployed to reduce their impacts without negatively impacting operations. Industrial sites are diverse and there is no blanket solution or method for addressing emissions across your value chain. There are however some tools and approaches that will assist in energy and emissions management across sectors.
Manage Industrial Energy Use in Your Value Chain
Before any energy management strategies can be implemented, it’s important that your suppliers understand their current energy use. An energy audit can help identify areas for improvement and prioritize energy-saving measures. This analysis can include an assessment of facility energy bills, equipment usage, and building systems such as HVAC, lighting, and insulation.
Some energy-saving strategies that may be appropriate for your supplier based on the audit results include:
- Upgrading Equipment: This may include upgrading lighting systems, HVAC systems, and other equipment such as motors and compressors that will reduce energy use and costs.
- Building System Optimization: Optimizing building systems can also lead to significant energy savings. One strategy is to perform regular maintenance on HVAC systems to ensure they are running at peak efficiency. This can include replacing filters, cleaning coils, and adjusting airflow. Another strategy is to optimize the building’s insulation to reduce energy loss.
- Implementing Automation: Automation can ensure equipment is only running when it’s needed. For example, automated lighting systems can turn off lights in unused areas of the facility.
- Employee Engagement: Actions like workplace sustainability programs that encourage mindful energy practices can be a powerful tool for reducing energy use in industrial facilities.
- Investment in Renewable Energy Resources: On-site generation, such as solar, can lower costs, reduce load on the local energy grid, and reduce local air pollution. Your supplier may be eligible for government incentives, such as tax credits or rebates, for installing renewable energy infrastructure.
- Building Energy Storage: Energy storage, such as battery systems, can reduce your suppliers’ energy costs and reliance on the grid, while also supporting grid resilience by returning excess energy to the grid during peak energy demand.
- Energy Management Systems: By installing energy monitoring and control systems, your supplies can better manage their energy use. These systems monitor energy use in real-time.
In addition to implementing energy saving strategies, you should encourage your value chain to develop monitoring and reporting processes to transparently track energy consumption at their industrial facilities. This will allow you to determine the effects of strategies you implement, help you understand and communicate these effects to stakeholders, and guide your future work.
Industrial emissions considerations also sit within broader climate justice considerations. It is important to encourage your suppliers to consider the impact their facilities have on nearby communities, such as through the health impacts of air and water pollution. Some steps that can be taken to mitigate impacts include engaging directly with nearby communities, implementing pollution control measures, and supporting community initiatives targeting positive social, economic, and environmental outcomes.
Reduce Emissions From Refrigerants and Industrial Gases in Your Value Chain
Refrigerants are chemicals used in cooling systems to transfer heat and keep spaces or products at lower temperatures. Industrial gases are used in various industrial applications, such as welding, manufacturing, and chemical processing. Common industrial gases include Sulphur hexafluoride (SF6), and Nitrogen trifluoride (NF3). Despite their importance, these refrigerants and gases have high global warming potential (GWP) and can lead to ozone depletion and other negative environmental impacts.
There are a number of specific actions you can encourage your suppliers to implement that will help reduce the effects — and costs — of refrigerants and industrial gases on their operations and the planet. These include:
- Leak Detection and Repair: Leak detection (and subsequent repair) can be performed using various methods, including visual inspection, ultrasonic testing, and using electronic leak detectors. Additionally, implementing a preventive maintenance program can help identify and address potential leaks before they occur.
- Retrofitting and Upgrading Equipment: Older equipment may use outdated refrigerants that are no longer allowed under current regulations, while newer equipment may produce less emissions or use alternative refrigerants and gases that have a lower global warming potential (GWP). Newer equipment is also often more energy-efficient, which can further reduce emissions and lead to cost savings over time.
- Proper Maintenance and Operation: Regular cleaning and maintenance can improve equipment efficiency and prevent leaks. Proper operation of equipment can also reduce the need for frequent repairs and replacements. Additionally, training employees on proper equipment operation and maintenance can improve equipment performance and longevity, while also reducing emissions.
- Recovery and Recycling: When equipment is retired or replaced, industrial gases can often be recovered and recycled for use in other systems. Proper disposal of refrigerants can prevent their release into the environment. Implementing a recovery and recycling program can help reduce emissions, costs and waste.
Because of the significant negative effects of refrigerants on the environment, there has been a recent push to make refrigerants more climate friendly. This includes using synthetic substitutes, such as hydrofluoroolefins, and natural alternatives such as air, water, ammonia, and carbon dioxide. While these technologies come with challenges, they present a cost-effective and sustainable solution to one of the core challenges facing industry today. In addition to the interventions listed above, your company and your suppliers may consider investing in innovation to reduce dependencies on high emitting refrigerants and gases and gain a competitive advantage.